
Because of the difficulty in controlling the formation of bainite, it generally has limited applicability, with the exception of austempering. It is very similar to tempered martensite in terms of hardness and toughness. It has a similar appearance to tempered martensite, with a feathery appearance (Figure 3). Two different morphologies of bainite were observed: upper bainite that formed just below pearlite, and lower bainite which forms at just above the M s Temperature. Bainite showed both the characteristics of pearlite and martensite, depending on the temperature of formation. Martensite is non-lamellar and not diffusion controlled. Pearlite contains a mixture of ferrite and iron carbide, and is diffusion controlled. This microstructure was unique in that it formed under continuous cooling or under isothermal conditions, with a structure that was similar to both martensite and bainite. This microstructure was named Bainite in honor of E.C. Bainiteĭuring the late 1920s, during studies of isothermal transformation of austenite, at temperatures above martensite formation, but below martensite transformation, Davenport and Bain discovered a microstructure that etched differently than martensite or pearlite. This can contribute to cracking before tempering. This retained austenite can transform to martensite upon application of lower temperatures, or by sudden shocks. This can cause significant amounts of retained austenite (austenite present at room temperature) to form. For most steels above 0.30 percent carbon, the M f temperature is above room temperature. The martensite finish temperature, M f, is also a function of carbon content and alloying elements. The martensite start transformation temperature, M s, decreases with increasing carbon content, and can be changed with different alloying elements. Only additional cooling can drive the transformation further.

Martensite transformation starts to transform at the martensite transformation temperature, M s, and ceases on reaching a given temperature. The mode of transformation is called athermal transformation (meaning without thermal activation). The conversion of austenite to martensite takes place continuously while cooling. If the volume expansion is too large, or occurs at a stress concentration, cracking can occur. This volume expansion is the major cause of distortion and warpage in steel parts. As the carbon content is increased, the volume expansion also increases. This stretch results in the volume expansion of the steel on fast quenching. As the carbon level of the martensite is increased, the stretch of the tetragonal axis also increases. This is essentially a Body-Centered Cubic structure that has been stretched along a diagonal between two opposite corners of the BCC structure. Figure 2: The body-centered tetragonal structure of martensite. Martensite forms a Body-Centered Tetragonal structure (Figure 2). The composition of martensite is exactly the same as the parent austenite. Because of the rapid cooling, diffusion is suppressed and carbon does not partition between ferrite and austenite. In iron-carbon alloys, austenite transforms to martensite on rapid cooling. Martensite was named after Adolf Martens by Floris Osmond in 1898. Martensite is the name used to designate the hard phase in quenched carbon and alloy steel.

In this column, we introduce two new microstructural phases: martensite and bainite. Figure 1: The decomposition of austenite, as a function of cooling rate.
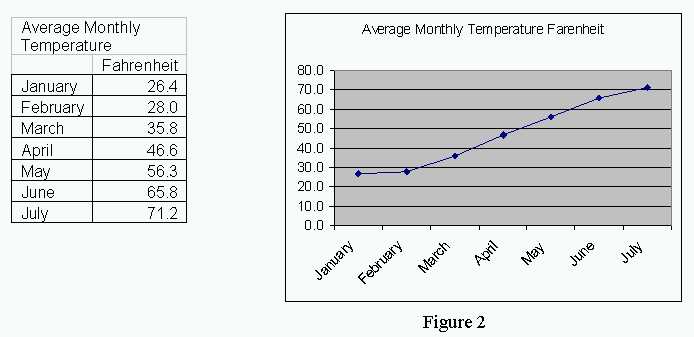
However, if the quench rate is too fast, then high residual stress and distortion may occur. Fast reactions will result in martensite transformation. Slow cooling will result in pearlite and ferrite. Transformations of austenite are dependent on the cooling rate. These curves are very important to start predicting the microstructure for a given alloy.
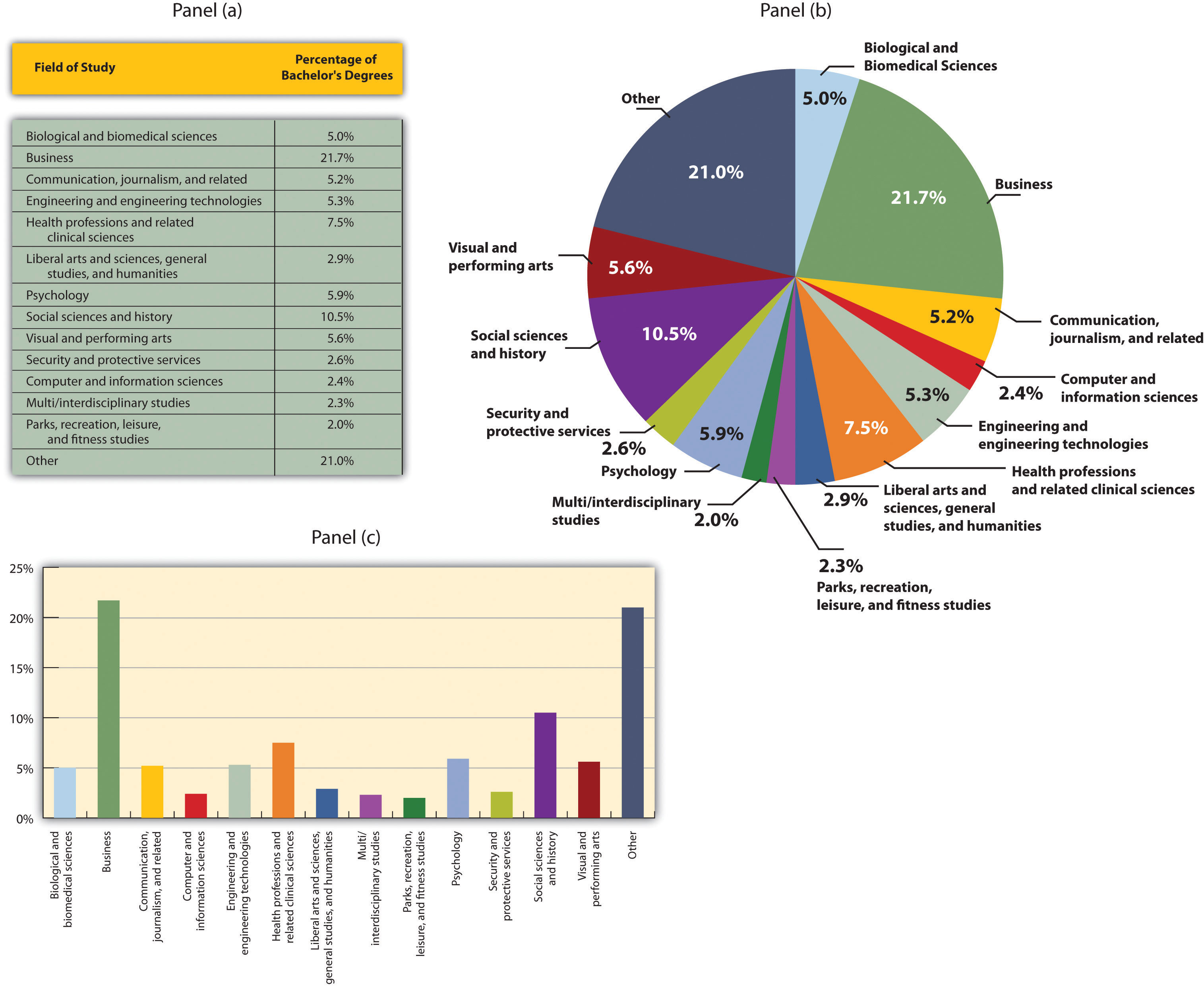
In this column, we build on those concepts and discuss the Isothermal Transformation or Time-Temperature-Transformation curves. This diagram allowed us to estimate the microstructure under non-equilibrium conditions. I n the previous column, we discussed the formation of the Iron-Carbon phase diagram.
